Finnish Innovation
High-level skill and production methods are used in manufacturing premium quality KINGI® metal roofing screws.
The KINGI® metal roofing screw us a Finnish innovation. Zinc coated steel roofs have been used since the 1950s, and factory-painted color coated metal steel roofs since the 1970s. At first, nails were used for attaching the lead sheets. Later, when the battery powered drills came to the market, screws became more popular. The advantage of the screws over nails is that they do not arise from wooden structures like nails quite often do. Another advantage is a more controlled tightening of the washer during the installation. Screws also ensure firmer and long-lasting fitting.
Metal roofing screws that do not fulfill even the minimum requirements of corrosion resistance painting have been used for over 30 years. Jorma Kinnunen decided to solve this problem. He invented a metal roofing screw that would not corrode and would be as long-lasting as Pural® coating, which he invented earlier in the 1990s. During the long product development process he combined the newest pre-treatment knowhow with the best knowledge of the powder painting, and the practical engineering of the screw design. As a result, an original Finnish innovation was born — the KINGI® metal roofing screw.
How KINGI® metal roofing screws are produced

WASHER
The washer is made from sea quality aluminum, which is stronger than usual aluminum and more corrosion resistant than normal aluminum. The secret of corrosion resistance of the sea quality aluminum is that magnesium is added to the aluminum-alloy. While the minimum strength of the basic aluminum is 55 megapascals (MPa), in the aluminum of the KINGI® metal roofing screws is 130 MPa. The recipe of the weatherproof EPDM-rubber used in the washer is developed especially for the metal roofing screws. The EPDM -rubber is vulcanized on the aluminum. The surface of the aluminum has been processed before vulcanizing.
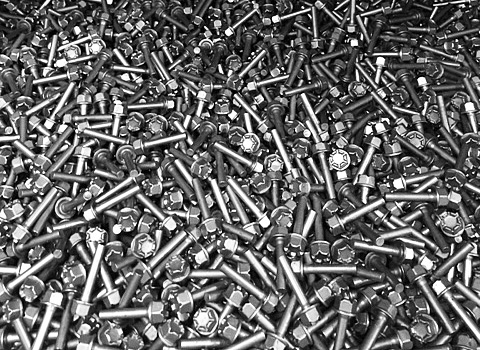
SCREW BLANK
The CrownD design head of the screw is created in two different processes. After which the FastFX™ screw tip is added.
The ready-formed screw blank is then hardened to create strength and surface hardness for a quick installation and long-lasting durability.
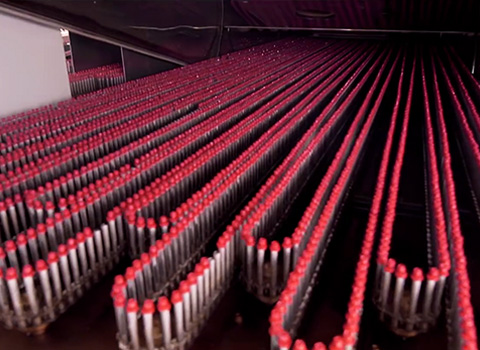
DURABL3-COVER
During the coating processes, the screw blank is first cleaned from protective oil used for the the transportation, and from other impurities. The cleaned screw blanks are processed by electric galvanizing. Zinc will protect the steel cathodically. The electric galvanizing makes a micro-coarse surface that will help the paint to have an anchoring effect. The zinc surface will additionally maximize the surface area for the paint to adhere. This way the adhesion of the paint and consequently the corrosion resistance of the coating system is increased. The thickness of the electric zincing is optimized so that it is sufficiently thick to secure the cathodic protection for the steel, but not too thick to avoid weakening the other properties of the screw.
In the final stage of the galvanizing process, a modern Silane-pretreatment is processed. It secures the adhesion of the paint and the corrosion resistance.
Radialco-design secures a sufficient coating thickness of the corners and edges. The corrosion resistance and the long-lasting look are finished by adding the patented Durabl3-coating. It is produced at the world’s first Durabl3-painting-line in Nurmijärvi, Finland.
The KINGI® metal roofing screw is born.
ISO 9001 – Quality Certificate
CONTROLLED QUALITY
The whole production process is tested and certified according to the ISO 9001 –quality standard. Quality assurance of the product is in accordance with standards SFS-EN ISO 3269 and SFS-EN ISO 10666:1999. Product quality is monitored continuously with the corrosion tests conducted by third-party research bodies.
In connection with manufacturing, the following quality control measures are taken:
- The dimensions of the screw are checked in two separate stages
- The drilling time of the screw is tested in three different stages
- The torsion strength is checked in two separate stages
- The thickness and quality of electric galvanizing is checked twice
- The hydrogen-brittleness risk is assessed
- The adhesion of paint is tested in two different stages
- The perfect fit of the screw into the socket is checked
In addition, selection of screws from every production batch are stored for at least 20 years for possible post-control. The quality of the coating system is followed continuously with the corrosion tests conducted by independent institutes.
Made in Finland
Over 50% of the production of the KINGI® metal roofing screws is done in Finland.
If you appreciate durability, quality, and the environment, then KINGI® is the screw for your metal roof.